激光熔覆技术作为一种先进的增材再制造技术,具有涂层与基体为冶金结合、能量集中、热影响区小、对基体损伤小、加工精度高等优点,能够实现复杂零部件的高效修复。在激光熔覆增材再制造过程中,再制造区域内形成的各种界面统称为再制造界面,该界面是再制造零部件的薄弱区域,为了使再制造零部件的性能达到甚至超过新品的性能,对该界面的缺陷进行分析是非常必要的。
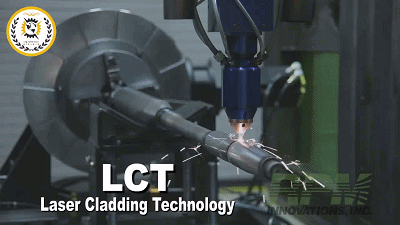
目前主要通过物理解剖法、数值模拟法及超声法、磁粉法、渗透法等无损检测方法获得零部件内部缺陷的信息,但是这些方法都存在不足之处,如对零部件造成不可逆的破坏;检测结果显示不直观、不准确;只对零部件的表面或近表面缺陷敏感等。
工业计算机断层成像(CT)技术是一种依据外部投影数据重建物体内部结构图像的无损检测技术,该技术可以非接触、非破坏性地检测物体内部缺陷,得到没有重叠的数字化图像,该技术不仅可以获得零部件内部缺陷的二维及三维空间信息,而且可以直观、准确地表达零部件内部缺陷的全方位信息。基于此将工业CT技术应用于零部件再制造界面的缺陷检测有其可行性和优势。
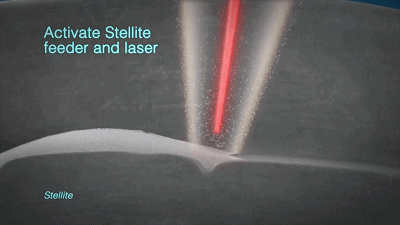
工业CT成像技术主要性能
工业CT
主要零部件包括:射线源、辐射探测器与准直器、数据采集系统、样品扫描机械系统、计算机系统及辅助电源和辐射安全系统等辅助系统等。
目前,用于评价工业CT成像系统性能的主要参数包括:检测试件的范围、射线源种类、扫描模式、检测时间、空间分辨率、密度分辨率及伪像等。
零部件再制造典型缺陷具有形貌复杂,尺寸较小,分布面积较广,缺陷边界不规则、不连续、多分支的特点,因此缺陷易被噪声所掩盖,缺陷的位置难以检测,缺陷的形成原因难以确定。当缺陷尺寸接近工业CT系统的检出限时,在CT图像上就会表现出容积效应;当缺陷表面与工业CT扫描平面不垂直时,工业CT图像中缺陷边缘有较宽的灰度过渡区,从而形成弱边缘;以上两点都会增大缺陷检测的难度。
针对再制造典型缺陷的上述特点,研究人员通过在工业CT系统中引入新的图像计算模型,或通过改善工业CT检测工艺参数,如切片厚度、探测器单元的微动次数、触发次数及图像矩阵等,有效降低了再制造典型缺陷图像噪声和伪像,提高了再制造典型缺陷图像显示的对比度,增强了再制造典型缺陷细节特征分辨率。
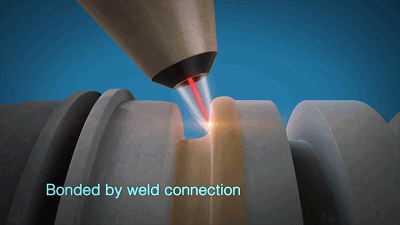
激光熔覆增材再制造典型缺陷形成机理
激光熔覆过程是一个快速成型的过程,即在极短的时间内发生快速熔化与快速凝固的过程,因此在涂层内部极易产生裂纹、气孔、夹杂等不良缺陷,严重影响再制造零部件的质量和性能。
裂纹形成机理
激光熔覆是一个速热、速冷的过程,该过程会产生局部受热不均匀,温度较高区域在冷却和凝固时会受到温度较低区域的约束,从而产生热应力;同时,该过程中基体表面材料、涂层材料都会经历固态变液态、液态又变回固态的变化,在这两个变化过程中,基体表面和涂层材料都会产生不同程度的体积收缩,必然会受到周边晶粒的牵制和约束,从而产生拉应力;当热应力或拉应力大于熔覆材料的抗形变能力时,就会产生裂纹。裂纹缺陷是激光熔覆增材再制造过程中最主要的内部缺陷,是对再制造零部件的质量和性能影响较大的一种缺陷,是激光熔覆过程中应重点消除的缺陷类型。
气孔形成机理
在激光熔覆过程中,当气体进入熔池或与金属表面氧化物发生还原反应生成气体时,由于熔覆涂层的凝固过程会在极短时间内完成,所以上述气体来不及从熔融液体中逸出,便会形成气孔。气孔缺陷是激光熔覆增材再制造过程中极易形成的内部缺陷,严重影响再制造零部件的力学性能,从而降低再制造零部件的使用寿命。
夹杂形成机理
基体表面和涂层材料所含的元素不同,其所具有的凝固点也不同,在激光熔覆的过程中,低熔点元素先熔化,高熔点元素后熔化,且可能存在未完全熔化的情况,在后续冷凝过程中,熔覆涂层中可能产生夹杂;在激光熔覆的冷却和凝固过程中,高熔点元素先凝固,低熔点元素后凝固,且低熔点元素会随着固液界面的上升而移向上层,因此熔覆涂层表层以低熔点元素为主,元素成分不均匀,进而导致熔覆涂层的组织中产生夹杂;以上两种情况下产生的夹杂缺陷都为裂纹缺陷的萌生提供了源头。
工业CT成像技术在典型缺陷检测中的应用
裂纹缺陷的检测与研究
零部件内部微观裂纹会随着零部件服役过程中的载荷作用与变形而不断变化,最终会发展为宏观裂纹,并造成零部件的破坏,甚至会导致灾难性事故。因此,检测零部件内部的裂纹缺陷及研究零部件服役过程中内部裂纹缺陷的演变规律,对保证零部件质量具有重要意义。目前,国内外学者利用工业CT成像技术从不同方向对内部裂纹缺陷的演变规律及扩展机理进行了大量研究。
BUFFIERE等早在20世纪90年代就在欧洲同步辐射实验室(ESRF)借助CT设备对碳化硅颗粒增强铝基复合材料的疲劳裂纹扩展行为进行了分析,标出了微米级裂纹分布。通过图像重建得到了三维裂纹体,测定了裂纹初始形核角度。
SCHILLING等进一步论证了采用CT断层成像技术观测裂纹等缺陷的可行性。
PENUMADU等通过高分辨CT设备探明了碳纤维增强复合材料裂纹产生的原因,采用OCTOPUS软件对图像进行处理,同时选择滤波反投影法实现了裂纹缺陷的三维重建。
重庆大学多年来致力于工业CT扫描图像重建算法的改进以及该技术在材料领域的推广应用。根据裂纹不同阶段的尺度差异,提出将裂纹萌生、扩展至断裂的整个过程分为3个阶段:显微尺度微观裂纹、CT尺度裂纹和宏观裂纹,为基于工业CT设备研究裂纹进行了较为科学的分类。
西北工业大学在采用工业CT技术检测裂纹扩展行为方面进行了较为深入的探索,提出了一种基于CT图像密度场的疲劳短裂纹群扩展行为监测方法,利用自主研发的CT Framework系统实现了裂纹群的三维可视化。
东南大学采用工业CT研究了零部件破坏过程中宏微观裂纹缺陷的演化特征,并提出了多尺度缺陷表征方法,能够较好地描述微观裂纹到宏观缺陷的多尺度演化过程,如图1所示。从图1可以看出,零部件变形过程中,裂纹演变过程为内部裂纹的萌生、扩展及聚合,主要表现为裂纹扩展和聚合,同时会伴随有部分新的裂纹萌生,而萌生的位置常常会在裂纹分布相对较少的地方。随着零部件的变形,裂纹会集中在一个带状区域,其他区域相对较少,零部件最终也会从该带状区域发生断裂。与零部件中间位置的裂纹相比,边缘的裂纹扩展速度更快,往往更容易造成零部件的断裂。
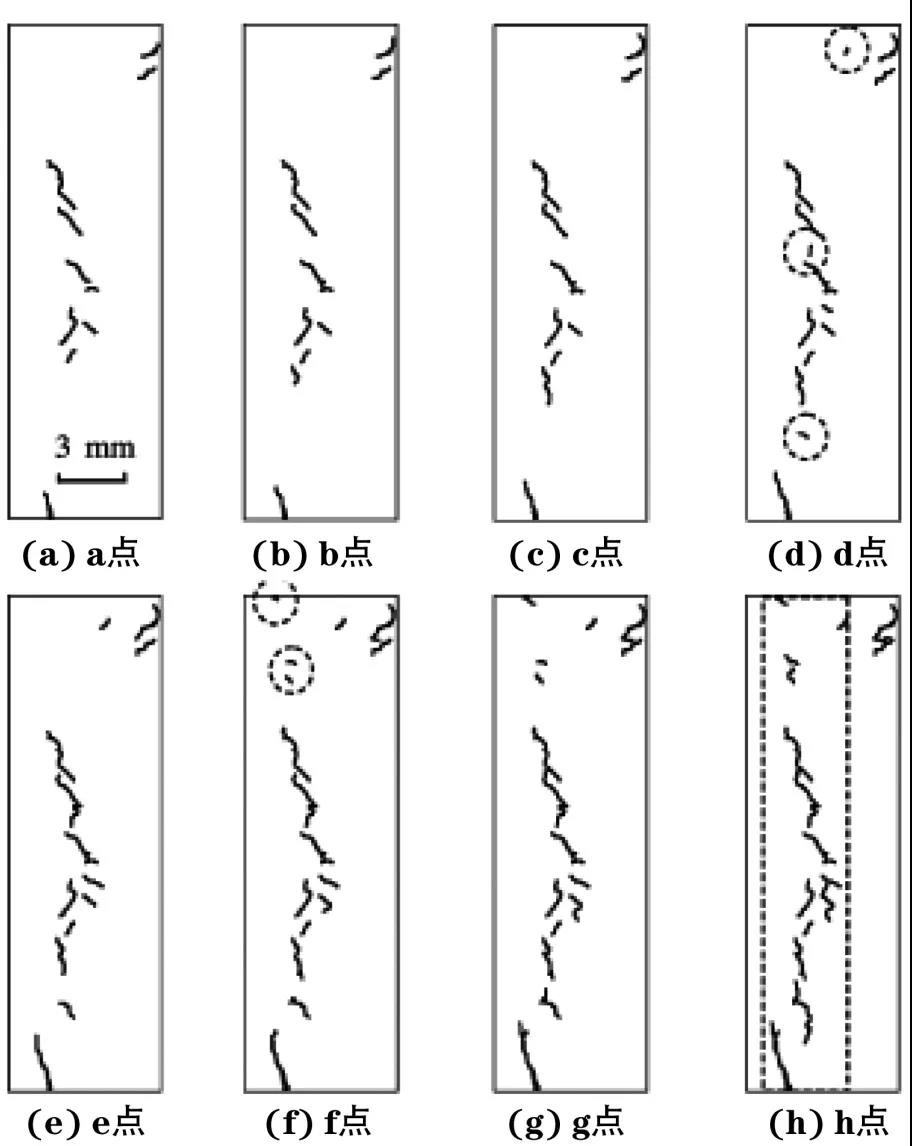
图1 零部件变形过程中微观裂纹扩展过程
气孔缺陷的检测与研究
气孔是零部件内部缺陷的主要形式之一,其体积与位置分布随机性较大,在外加载荷的作用下,气孔缺陷会不断变化,最终会导致零部件整体结构的破坏。
赵超凡等采用工业CT研究了零部件在拉伸试验过程中宏微观气孔缺陷的演化过程,研究结果表明,随着零部件变形的增加,其内部缺陷会产生两种情况:新气孔的萌生和原气孔的增长。基于以上研究结果,提出了多尺度气孔缺陷表征方法,很好地描述了从微观气孔萌生、增长到零部件失效的全过程,如图2所示。从图2可以看出,随着零部件变形的加剧,零部件的焊接处不断产生新的气孔,分布位置没有固定规律,而原有气孔的体积也会增大。在零部件变形过程中,气孔缺陷的数量和体积均有所增加,而其形状没有明显改变。
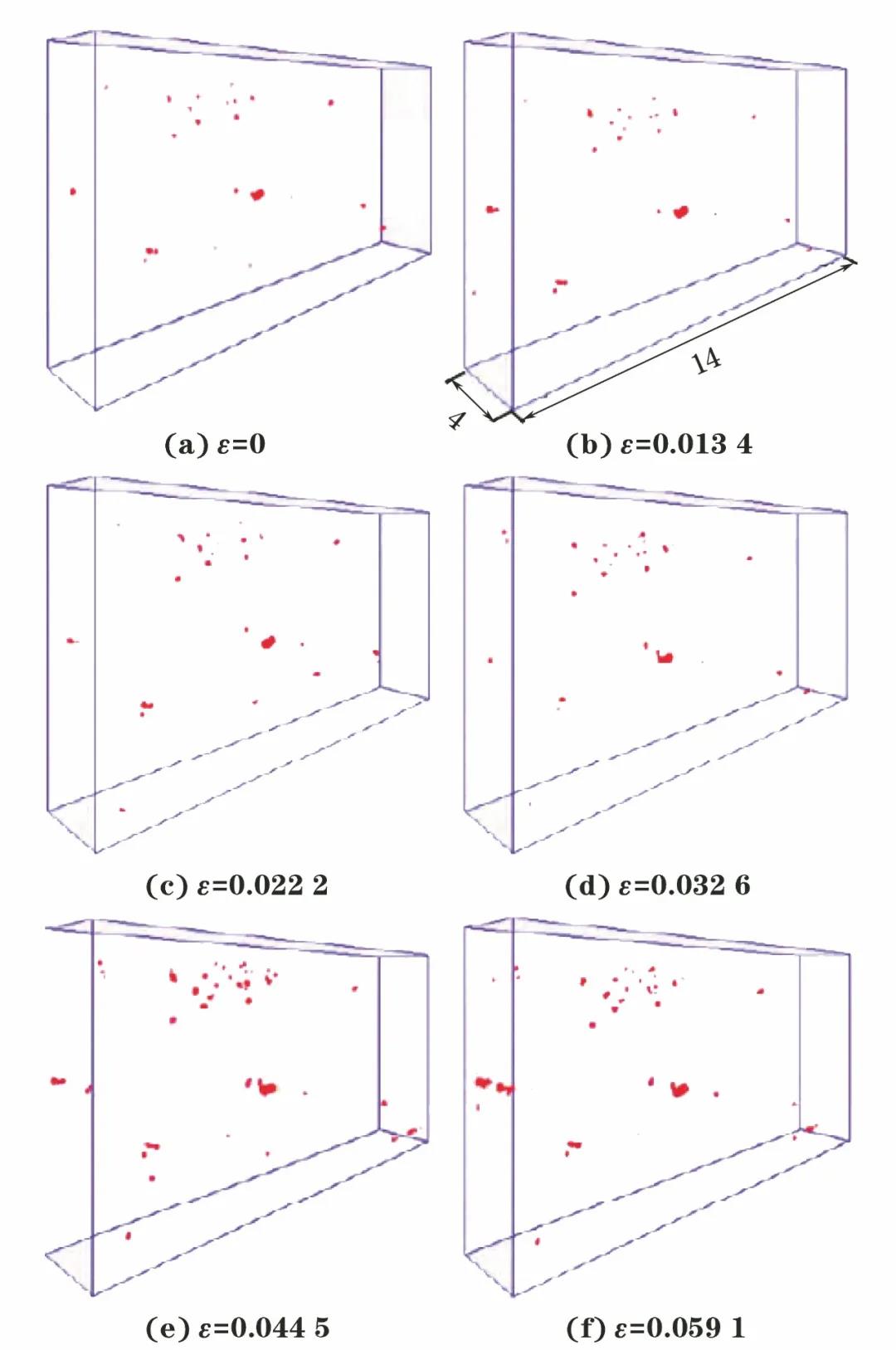
图2 零部件变形过程中气孔演化过程(ε为应变)
POLOZOV等通过选区激光熔覆法制备了钛合金化合物,并利用工业CT技术检测其内部孔隙的尺寸与分布,从而研究了合金的致密性。结果表明合金内部孔隙尺寸为32μm,孔隙率只有0.7%,制备的钛合金化合物是一种全致密材料。
夹杂缺陷的检测与研究
目前,高铁齿轮箱体材料多为铸件,铸件中存在各种尺度和维数的缺陷,在服役过程中,微结构形态、缺陷分布和形貌、界面特性、孔隙率等都极大地影响着材料宏观整体韧性、强度、硬度等力学性能。铸件缺陷主要以夹杂缺陷为主,具有复杂性,一般无损检测方法不能对其进行直观、高效地检测,而工业CT成像技术可以清晰地检测出铸件夹杂缺陷的立体结构状况,直观地显示出夹杂缺陷的位置及形状。
艾轶博等利用三维工业CT成像技术对高铁齿轮箱体内部缺陷进行检测,指出夹杂缺陷所占比例最大,通过设计试验获得了箱体材料的夹杂缺陷的三维图像,如图3所示,实现了对高铁齿轮箱体内部缺陷自动、准确地分类和识别,为实现高铁齿轮箱体材料内部缺陷的自动识别提供了技术支持。
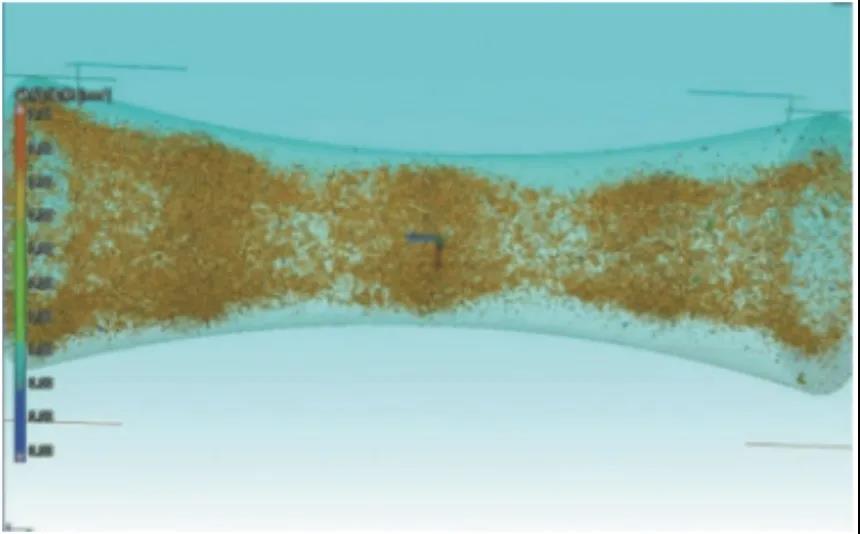
图3 高铁齿轮箱体内部夹杂缺陷三维图
混凝土,尤其是水泥混凝土已成为现代工程(建筑、道路、桥梁等)最重要的材料之一。混凝土在使用过程中由于各种原因其内部会产生夹杂缺陷,影响混凝土的力学性能,带来工程安全隐患。
ZHU等认为工业CT成像技术是测试混凝土微观夹杂缺陷的重要手段,通过观察混凝土同一区域在不同压力下的CT成像,比较CT成像的灰度值,可以推导出该区域微观夹杂缺陷的演变情况,从而为完善混凝土的加工和制备工艺,提高混凝土的质量提供理论支持。
由于复合材料具有低线胀系数、高比模数、高比强度、防腐耐蚀等优点,已广泛应用于武器装备、航空航天、汽车等领域。但复合材料是由两种或两种以上不同性质的材料通过化学或物理方法制备而成的,在应用过程中会由于原材料中自带杂质或油污、加工工艺技术问题及操作不当等因素产生以夹杂、分层为主的各种缺陷,因此工业CT成像技术对控制和提高复合材料制品的质量,改善生产工艺有指导意义。
赵付宝等利用工业CT成像技术有效地检测出了树脂基复合材料制品的内部缺陷,并能精确地测定缺陷的位置与几何尺寸,如图4所示。图4(a)中发亮的部位是复合材料制品内部的夹杂缺陷,该夹杂缺陷的密度大于原材料的密度,所以其灰度比周边大;但由于大多数材料的密度较为接近,所以无法只依据CT图像对夹杂的类别做出判断。图4(b)中黑色的连续不规则的线条为复合材料制品内部的分层缺陷。
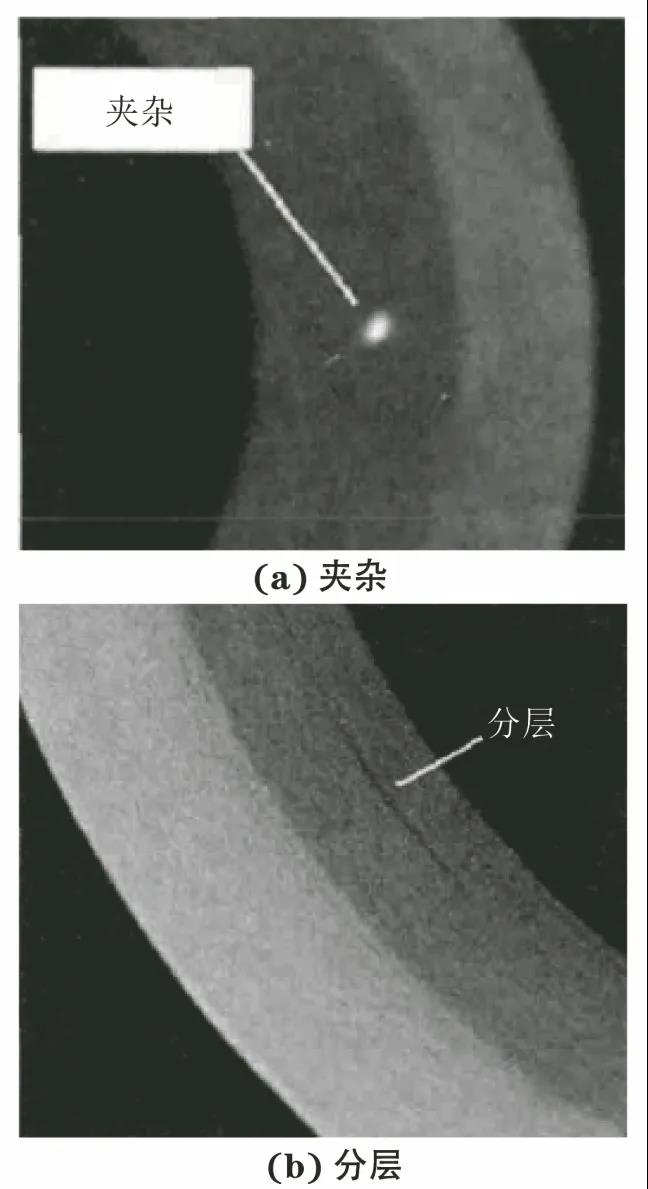
图4 复合材料制品内部缺陷外观
工业CT成像技术在再制造界面缺陷研究中的难点
在激光熔覆增材再制造过程中形成的再制造界面即有同质界面又有异质界面,界面成分众多,组织结构庞大,常用的无损检测技术无法准确、直观地确定再制造界面的缺陷。工业CT成像技术不受零件结构、组成成分与表面状态等限制,可以准确表征出零部件的内部结构信息,为激光熔覆增材再制造界面的缺陷检测提供了最佳检测手段。
在实际应用中,激光熔覆增材再制造零部件自身形状不规则;再制造界面情况更为复杂:界面材料成分繁多;界面组织结构复杂;界面缺陷种类较多、尺寸较小、分布面积较广;界面缺陷的边界不规则、不连续、多分支。
而工业CT成像系统自身也有局限性:检测对象的尺寸和材料必须与所用设备的运转系统和射线的能量相匹配,能量太低无法穿透检测对象,能量太高会使检测对象曝光过度;检测对象的几何特性影响工业CT成像系统的空间分辨能力与密度分辨能力;工业CT图像中的每个点都要经过大量计算模拟,在模拟过程中如数据处理不当,就会产生与检测对象不相符的伪像。因此,提高工业CT成像技术在再制造界面缺陷分析研究中的空间分辨率、密度分辨率,及改善检测过程中的伪像是广大学者研究的难点与重点。
工业CT成像技术在再制造典型缺陷研究中的展望
为了使激光熔覆增材再制造零部件的性能达到甚至超过新品的性能,满足再次服役的要求,必须对其进行缺陷检测。工业CT成像技术有望成为再制造典型缺陷分析研究中一种重要的无损检测手段,其研究发展方向主要涉及以下几个方面:
1 提高工业CT技术检测精度。
基于再制造零部件内部及再制造界面的典型缺陷的特点,工业CT成像技术的迅速发展将成为再制造典型缺陷分析研究实现突破性进展的前提条件,只有工业CT成像技术拥有更小的尺寸精度、更高的分辨率、更精准的重建算法及更有效的图像处理技术,才可能实现再制造零部件内部及再制造界面缺陷的智能化检测、自动化识别与分类。
2 大型再制造零部件的缺陷检测。
高端大型再制造零部件的体积庞大、结构特殊、工艺复杂,常规的无损检测手段均无法准确获取产品内部的结构和缺陷信息,工业CT成像技术是大型再制造零部件不可替代的缺陷检测手段。大型再制造零部件由多种材料构成,内部结构复杂,对缺陷检测技术要求极高,如成像视野直径要大(超过2m)、缺陷识别种类多、检测精度要求高等,导致大型再制造零部件缺陷检测面临着工业CT成像系统的高分辨率与大扫描直径、探测效率、扫描速度、动态范围之间的矛盾。通过增强工业CT成像系统的射线源,完善系统的探测器设计,提高系统的扫描效率,引入合理的图像重建运算方法,可确保工业CT成像技术实现对大型再制造零部件内部缺陷的高效识别与检出。
3 降低检测成本,扩大使用范围。
工业CT成像装置本身造价高于其他无损检测设备,且该技术检测过程较耗时,检测效率相对较低,检测成本较高,导致其使用范围受到限制。通过在工业CT成像系统中引入新型计算模拟技术,提高了工业CT成像技术的检测效率,降低了检测成本,扩大了工业CT成像技术的应用领域。