一、空洞检测
(a)是当钢管内核心混凝土与钢管壁结合紧密,核心混凝土均匀密实。在混凝土介质中超声波就沿直线从发射端传播到接收端,用时最短,声波能量衰减最小。
(b)表示当钢管壁与其内核心混凝土发生脱空。超声波首先沿钢管壁传播,在脱空边缘发生绕射,再从绕射点沿直线传播到接收端。
(c)是由于钢管内核心混凝土不密实,造成了超声波的散射,最短的传播路径变成了曲线。
(d)是当钢管混凝土内存在空洞,且空洞正好位于超声波从发射到接收的路径上,超声波会在空洞的边缘发生绕射,使传播声时变长。
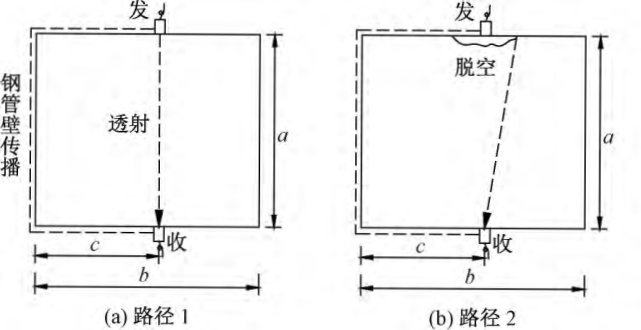
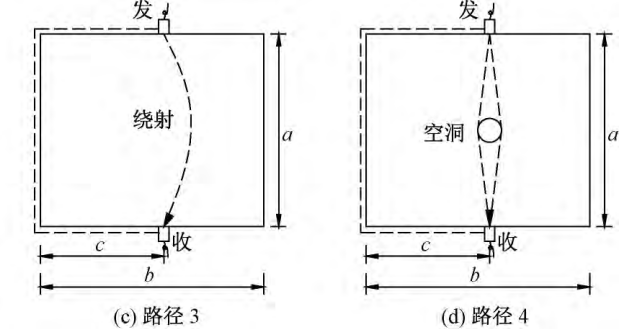
利用首波声时的长短可判断声波的传播路径: 首波声时长说明传播路径长,首波可能绕射缺陷或沿钢管壁传播; 首波声时短说明传播路径短,首波可能透射混凝土沿直线传播。
二、裂缝深度检测
以超声时距法为例:
使用具有显示波形功能的超声波检测仪,测出并分析在混凝土内部传播的超声波信号的主频率、波幅、传播声速和声时等声学参数,通过分析这些声学参数的变化,计算出混凝土内部裂缝深度状况。
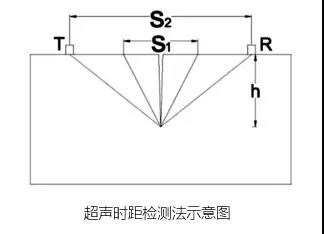
通过对两个不同检测距离的测点进行裂缝检测,读取超声波在裂缝试块中传播过程的时间,可以得到超声波传播过程中的传播声时、检测距离和裂缝深度,且依据公式(1)所示关系,当S2=2S1时,即为BS-1881标准法,其计算方法如公式(2)所示:
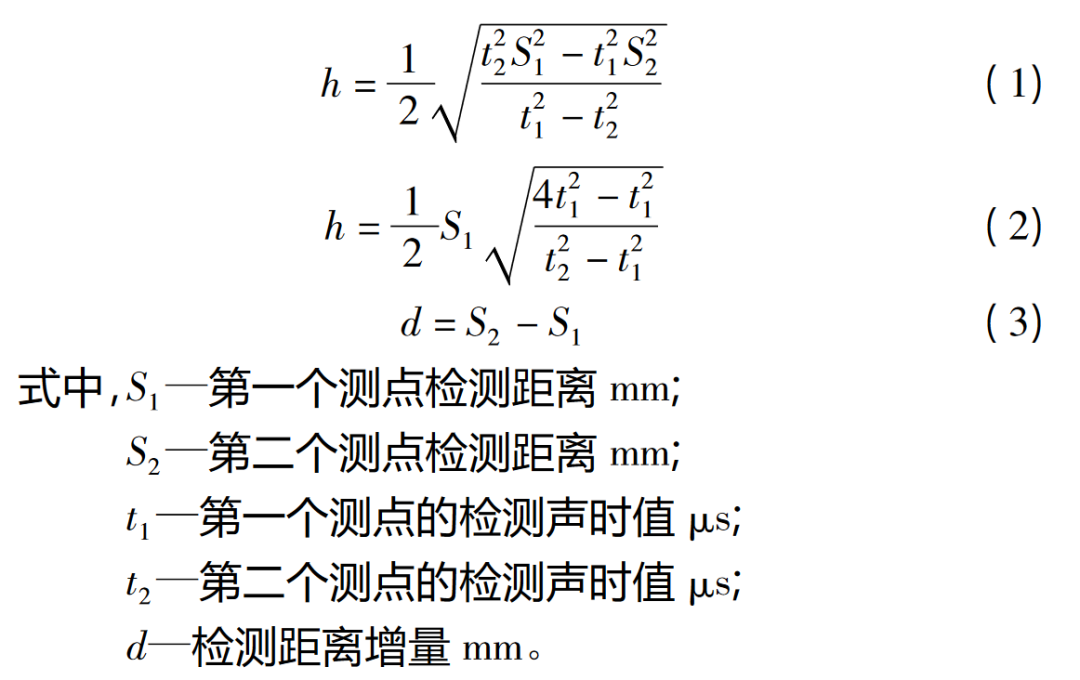
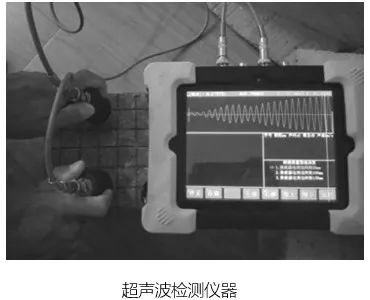
三、混凝土结合面质量检测
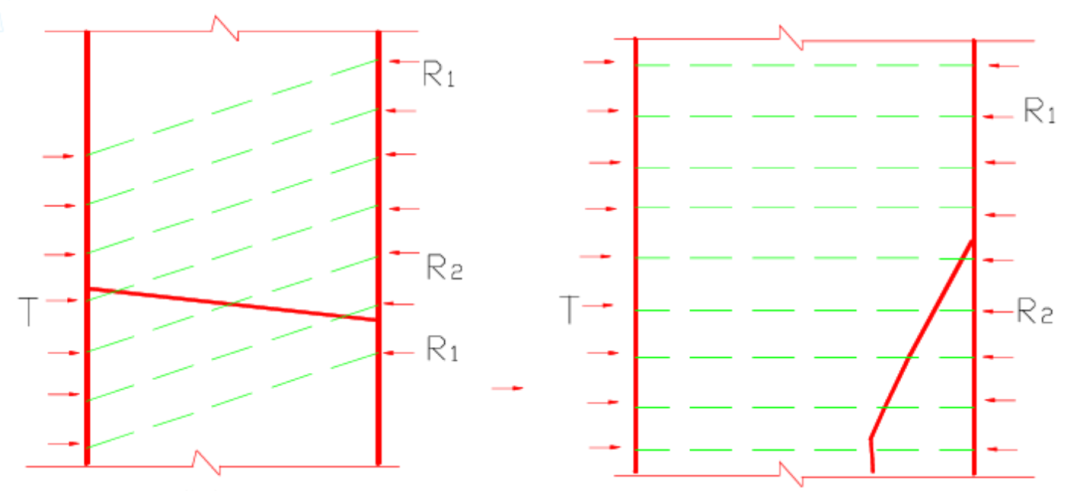
按布置好的测点, 分别测出每个点的声时、波幅和主频值。
将测位各测点的波幅、声速和主频值由大到小按顺序排列,即X1≥X2≥······≥Xn≥Xn+1≥······,将排在后面明显小的数据视为可疑,再将这些可疑数据中最大的一个(假设为Xn)连同其前面的数据算出声学参数平均值mx、标准差sx。

按下式与表格计算异常情况的判断值X0。
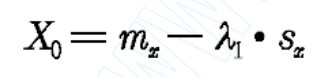
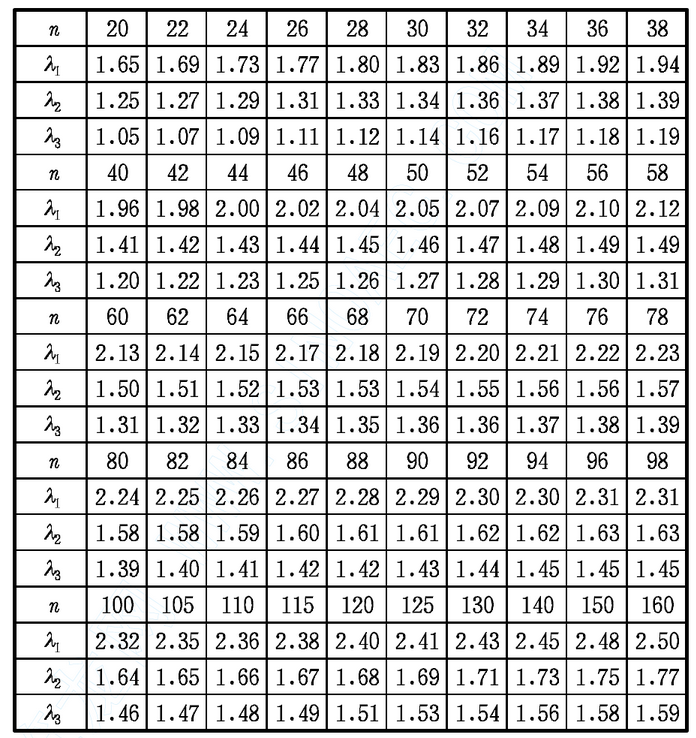
当Xn≤X0时,Xn及排列于其后的各数据均为异常值,去掉Xn,再用X1 - Xn-1进行计算和判别,直至判不出异常值为止;当Xn>X0时,应再将Xn+1放进去重新进行计算和判别。
当测位中判出异常测点时,可根据异常测点的分布情况,按下式进一步判别其相邻测点是否异常

其中当测点布置为网格状时取λ2 ,当单排布置测点时将λ1、λ2、λ3按表取值。
当通过结合面的某些测点的数据被判为异常,并查明无其他因素影响时,可判定混凝土结合面在该部位结合不良。
检测混凝土表面损伤层厚度时,可选用频率较低的厚度振动式换能器。
测试时激发换能器T应该耦合好,保持不动,将接收换能器R依次耦合在间距一定的各测点1、2、3 ······等位置上,读取相应的声时值t1、t2、t3 ······,并测量每次T、R换能器内边缘之间的距离l1、l2、l3 ······

检测损伤层厚度示意图
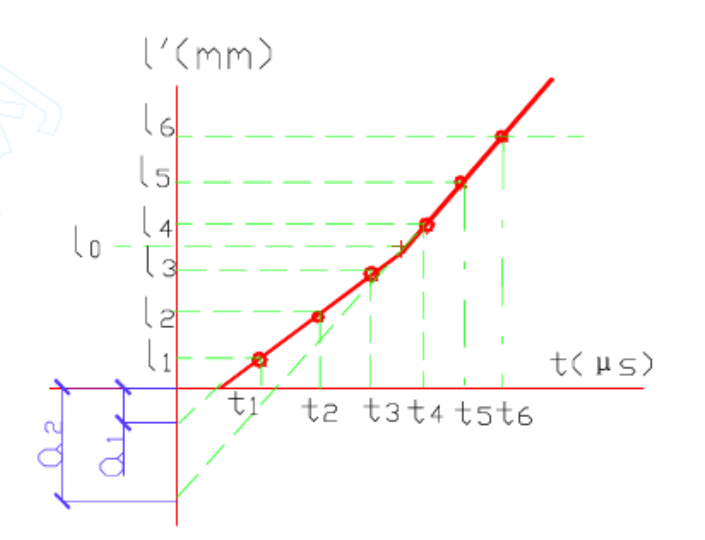
l-t坐标图
由图可得到声速改变所形成的转折点,该点前、后分别表示损伤和未损伤混凝土的相关直线,求出回归直线方程 :
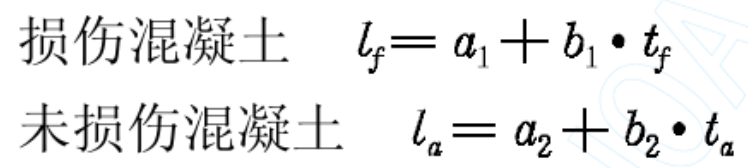
最后可计算出损伤层厚度hf :